What Are Refinery Turnarounds and Shutdowns?
Refineries, the workhorses of our modern world, transform crude oil into the fuels that power our lives.
But like any complex machinery, they require meticulous care to maintain peak performance and ensure safety.
This is where the turnaround comes in, a critical period of planned maintenance often overlooked yet vital to the refinery's long-term health.
Unlike flashy shutdowns in the headlines, turnarounds are precision-planned events.
Engineers, inspectors, and specialists meticulously prepare for months, assessing equipment, detailing tasks, and coordinating resources.
In this guide, we'll explore the refinery turnaround process, covering everything from careful planning to the essential tasks and collaborative efforts that make sure the transition from operation to maintenance goes smoothly.
What Are Refinery Turnarounds?
Refinery turnarounds are planned and periodic shutdowns of refinery operations, undertaken every three to five years.
These strategic events involve preventive maintenance, renovations, and upgrades to ensure safe, competitive, and compliant refinery operations.
During turnarounds, specific units or the entire refinery may be temporarily taken offline, allowing for thorough inspections, testing, and necessary repairs.
The planning and execution of refinery turnarounds are meticulously coordinated efforts, often scheduled during periods of low production when skilled labor is readily available.
The duration of turnarounds varies, ranging from a few weeks to months, depending on the project's scope and any unforeseen issues encountered.
If problems are identified during the inspection, the turnaround duration may be extended to address issues comprehensively.
What is the Difference Between Shutdown and Turnaround?
In industrial settings, particularly within refineries, the terms "shutdown" and "turnaround" are often used interchangeably, but there are nuanced differences.
A "shutdown" temporarily halts operations in a specific part of a facility, planned for maintenance or unplanned due to emergencies. It's shorter in duration and affects a specific unit.
A "turnaround" is a comprehensive, planned shutdown for the entire facility or a major unit. It involves preventative maintenance, upgrades, or unplanned extensive repairs, lasting weeks to months and causing complete production halts.
Adding to these, there's a less frequently mentioned interruption: "outages." It is any unplanned interruption caused by equipment failures or unforeseen events. Its impact varies depending on duration and severity, potentially leading to significant disruptions and financial losses.
Why Turnaround Times are Important for Refineries?
Turnaround time = money!
Every minute a refinery is offline translates to lost production and revenue. For a large refinery, even a single day of downtime can cost millions of dollars in missed sales. This can have a significant impact on the company's financial performance.
Turnarounds themselves are expensive undertakings. They require significant manpower, materials, and specialized equipment.
While the refinery isn't producing, expenses like salaries, security, and overhead still accrue. This further erodes profits during the turnaround period.
Beyond the financial aspect, turnarounds involve extensive maintenance and repairs, often with hazardous materials and equipment.
Reducing the turnaround time becomes crucial not only for financial reasons but also for minimizing personnel exposure to potential risks
In a competitive market, quick turnaround times help refineries swiftly resume operations, regain market share, and stay ahead of the competition.
What Are the Phases of a Refinery Turnaround Procedure?
Refinery turnaround, a carefully orchestrated process, unfolds in distinct phases, each with specific tasks and goals.
Phase 1: Scoping and Planning (Months Before Shutdown)
The initial phase starts with a thorough risk assessment, analyzing potential hazards like equipment failures and environmental concerns.
The team then outlines the turnaround by specifying equipment and processes. This plan serves as the blueprint, guiding resources, and priorities.
With the plan set, detailed work orders are crafted as task scripts, including materials and timelines.
Budgeting follows, ensuring optimal financial management. The scheduling process becomes crucial, creating a detailed timeline that guides every activity. Open communication is established between teams to ensure smooth decision-making.
Safety takes center stage, with thorough training ensuring personnel can navigate the turnaround safely, adhering to protocols and procedures.
Phase 2: Preparation and Pre-Shutdown (Weeks Before Shutdown)
As the turnaround date nears, the refinery transforms into an examination room. Technicians focus on inspecting and cleaning equipment, scrutinizing every component for potential issues before maintenance.
Material procurement ensures necessary supplies are readily available, like stocking a well-prepared pantry. Simultaneously, the administrative process begins, covering permitting and regulatory compliance to ensure adherence to environmental and safety regulations.
Isolation and depressurization procedures are executed, creating a safe working environment for technicians during the shutdown. Inventory and tagging processes prevent mix-ups, labeling each equipment part for smooth reassembly post-maintenance.
Safety drills and emergency preparedness rehearsals enhance readiness, minimizing risks and maximizing response efficiency during the actual shutdown.
Phase 3: Shutdown and Equipment Access (Turnaround Days)
On turnaround day, the refinery gracefully enters its shutdown phase. Technicians secure equipment access and isolation, creating safe workspaces for maintenance within the broader shutdown.
Caution prevails during hot work, with meticulous management of sparks. Rigorous safety measures, including permits, minimize the risk of fire or explosions during welding or cutting.
Waste management and environmental controls are pivotal, minimizing the turnaround's impact. Proper procedures ensure responsible resource stewardship, safeguarding the surrounding ecosystem.
Phase 4: Maintenance and Upgrades (Turnaround Weeks)
The repair crew steps into the spotlight, armed with diagnoses. Technicians adeptly replace worn-out parts, fix malfunctioning components, and address identified issues with meticulous precision.
The turnaround isn't just about repairs—it's a chance for upgrades and modifications. New equipment, improved processes, and technological advancements seamlessly enhance efficiency, capacity, and overall refinery performance.
Quality control is paramount, with meticulous checks and non-destructive testing ensuring everything stays in tune, and verifying the integrity and functionality of repaired and upgraded equipment.
Each maintenance step is carefully recorded. Documentation maintains a detailed log of activities, repairs, and test results, providing valuable insights for future improvements and contributing to ongoing refinery success.
Phase 5: Restart and Post-Turnaround (Weeks After Shutdown)
In the final stage, thorough pre-startup checks ensure a safe and efficient restart. Every system undergoes meticulous examination, eliminating room for last-minute surprises. Once all systems are gone, the controlled startup and optimization phase begins.
The refinery gradually awakens, fine-tuning processes for optimal production and efficiency. The performance continues with a comprehensive post-turnaround evaluation and lessons learned session, identifying areas for improvement and documenting valuable insights.
The curtain closes with the preparation of final turnaround reports, featuring cost analysis, performance data, and recommendations. These reports are crucial tools for optimizing future turnarounds.
How Drones Can Help Significantly Reduce Refinery Turnaround Times?
Traditional inspection methods are often slow, manual, and require extensive scaffolding, leading to increased downtime in refinery turnaround processes.
JOUAV introduces a revolutionary drone ecosystem designed to address these challenges, offering cutting-edge technology and an intelligent inspection platform. This combination empowers refineries in several key ways:
- Reduce turnaround time by up to 30%
- Minimize safety risks for your workforce
- Cut inspection costs by 20% or more
- Higher data processing efficiency
CW-15 VTOL Drone
This fixed-wing drone with VTOL capabilities is ideal for covering vast refinery complexes. With a 1200-hectare coverage area and a 180-minute flight time, the CW-15 efficiently captures comprehensive data.
It creates detailed 3D maps, inspects pipelines for leaks and corrosion, and patrols the perimeter for security threats, offering real-time situational awareness.
PH-7E Multirotor
This agile drone excels in detailed inspections of critical assets like heat exchangers, reactors, and distillation towers. Its hovering capabilities allow for precise data capture, even in hard-to-reach areas.
The PH-7E also monitors hot work activities from a safe distance, ensuring safety protocols are followed. In emergencies, its rapid aerial assessment expedites response times for first responders.
JOUAV Intelligent Inspection Platform
The platform is crucial for boosting efficiency, offering closed-loop inspections with automatic analysis through accurate machine learning algorithms (over 90% accuracy). These algorithms swiftly identify issues like corrosion, leaks, vegetation encroachment, and security threats.
Upon detection of anomalies, the system initiates work orders in the maintenance system, assigning tasks to relevant personnel. Users can effortlessly track the progress and completion of work orders, while the platform supports ongoing tracking and analysis for continual improvement and prevention of similar incidents.
For streamlined data management, the platform provides secure cloud-based storage, organizing images, sensor readings, and annotations.
Sharing dashboards and reporting tools facilitates communication and collaboration among inspectors, engineers, and maintenance personnel.
Additionally, the platform enables real-time dynamic monitoring of information related to drones, personnel, and vehicles.
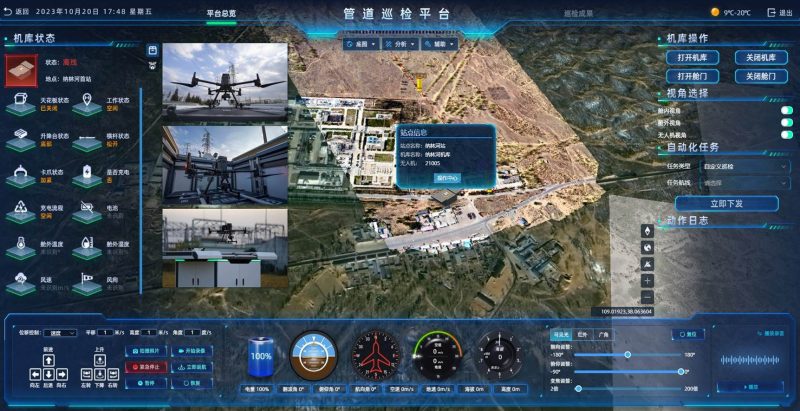
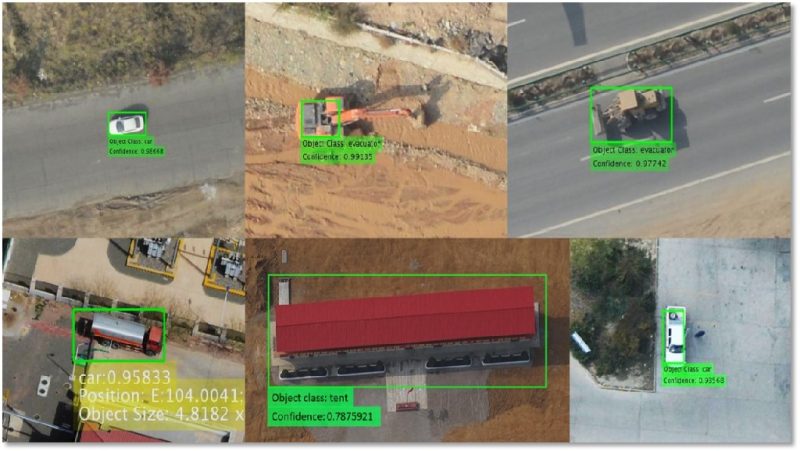
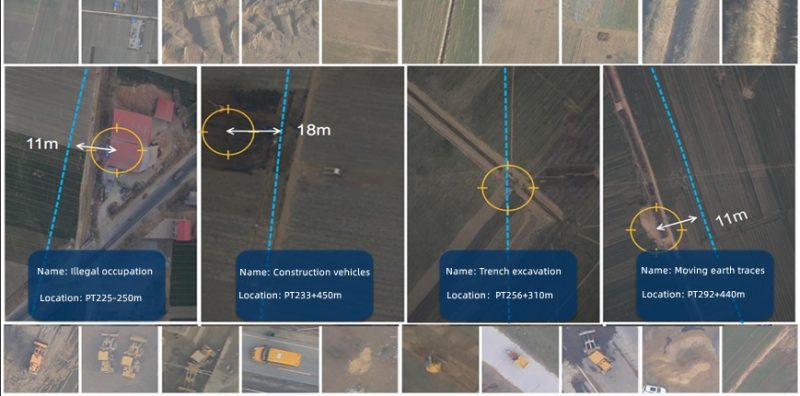
What Are Risks of Refinery Turnarounds and How to Help Increase Safety?
A turnaround is far from a routine workday; it's a complex event encompassing up to 150,000 different activities. Several key factors contribute to increased risk during a turnaround:
Increased Workforce
The influx of additional workers during a turnaround, including contractors, agency personnel, and temporary staff, significantly alters the workforce dynamics. This surge, sometimes doubling or tripling the regular workforce, introduces an elevated level of risk.
Safety Tips:
- Conduct comprehensive safety inductions for all new personnel, emphasizing site-specific protocols and emergency procedures.
- Implement a buddy system, pairing experienced workers with newcomers for guidance and support.
- Ensure clear and consistent communication through regular briefings, signage, and readily available safety information.
Additional Machinery and Vehicles
To facilitate the cleaning, repair, and reinstatement of machinery, an array of additional equipment and vehicles is mobilized during a turnaround.
This includes cutting and welding apparatus, as well as machinery for power washing and deposit softening.
The introduction of more machinery not only raises the exposure to gases but also amplifies the risk of collisions due to the increased presence of vehicles.
Safety Tips:
- Conduct thorough risk assessments for all brought-in equipment, ensuring proper maintenance and adherence to safety regulations.
- Implement traffic management plans, including designated walkways and clear markings for vehicle movement.
- Enforce mandatory use of appropriate PPE, including hearing protection, respirators, and high-visibility vests.
Confined Spaces
Executing a turnaround involves accessing areas of the plant that are not conventionally designed for human occupation.
Workers venture into confined spaces such as shafts, manholes, tunnels, and tanks, intensifying the potential for toxic gas build-up or oxygen deficiency.
These confined spaces pose various challenges, including restricted movement, reduced lighting, communication difficulties, and potential rescue complexities.
Safety Tips:
- Conduct thorough permit-to-work procedures before any confined space entry, assessing risks and implementing necessary controls.
- Continuously monitor oxygen levels and gas concentrations within the confined space.
- Utilize proper ventilation systems and maintain clear communication with personnel outside the space.
Noise
The inclusion of additional machinery and vehicles during a turnaround inevitably results in elevated noise levels.
Studies indicate that hazardous worksite noise is prevalent, with workers in industries like oil and gas extraction facing a significant risk of hearing loss.
Safety Tips:
- Conduct noise level assessments and implement noise control measures like soundproofing and barriers.
- Enforce mandatory use of hearing protection devices like earplugs or earmuffs.
- Utilize alternative communication methods like hand signals or radios in areas with excessive noise.
Hot Work
Turnarounds often necessitate "hot work" projects, like welding, cutting, brazing, soldering, and grinding. These activities carry a potential risk of accidental ignition of flammable materials.
Additionally, there is the possibility of flammable gases leaking into the work environment from hot work equipment, further increasing the complexity and risk associated with such tasks.
Safety Tips:
- Implement strict hot work permit procedures, clearly defining authorized areas and precautions.
- Conduct thorough fire risk assessments before commencing hot work, removing or isolating flammable materials wherever possible.
- Provide fire extinguishers and fire blankets readily accessible in hot work zones.
Power Outages
During a turnaround, periodic power shutdowns are common, creating higher-risk conditions.
Studies indicate that a significant percentage of work-related accidents in manufacturing plants occur during maintenance outages.
Safety Tips:
- Develop and rigorously test comprehensive emergency response plans for power outages, including backup lighting and communication systems.
- Ensure temporary lighting solutions meet safety standards and are compatible with any hazardous materials present.
- Conduct regular safety drills that simulate power outages to familiarize personnel with emergency procedures.